Live2Ride
New member
- Joined
- Nov 24, 2003
- Messages
- 14
02 viper. I know they have heated carbs, but these are turned on. Twice last winter had problems with sled not running. Both times involved snowy conditions and riding prior to problem. Is there some recall or way to fix this....other than just covering screens.... heard there is a problem with fuel pumps and there are some mods that can be made......please let me know if you have any solutions to this problem. THANKS
Pray for snow!!!!
Pray for snow!!!!
Mtnviper
Member
If the carbs run out of fuel, (start and stall condition) after its been sitting for awhile. It could be the fuel pump is freezing up. The pump is bolted flat to the tunnel and can draw moisture in through the vent screen. I shimmed the pump up off the tunnel by using 5/16" rubber spacers and loctite on the nuts. I do not recommend siliconing the vent hole shut. That hole is there to vent pressure/vacuum off the back side of diaphram. With the vent plugged there is a very good chance you are reducing to maximum flow of the pump. On a stock Viper this may not be an issue, but if it's piped, it dosn't matter how big of main jets you put in. If the total fuel flow volume isn't there, she's going to burn a piston.
Fuel pumps that do not have a vent hole. Are designed to have a large enough cavity on the back side of the diaphram, to allow proper diaphram movement for the pump's rated flow capicity.
Fuel pumps that do not have a vent hole. Are designed to have a large enough cavity on the back side of the diaphram, to allow proper diaphram movement for the pump's rated flow capicity.
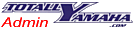
see the Tech Pages on the Fuel Pump Issue...
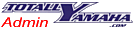
all 2003 vipers had vent holes in the fuel pump, if you dont you dont but thats strange!!!
ducky_d
Member
- Joined
- May 21, 2003
- Messages
- 32
Ok, 2002 and 2003 has venthole and 2004 does not ?
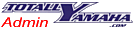
that vent issues. I wouldnt worry about...run your pipes...I would like to see hard data on this.....maybe I am wrong 

Mtnviper
Member
It would be interesting to see some flow data, plugged and unplugged. I do know that hole was put there for a reason, for venting the back side of the diaphram. The vent allows air to escape and be drawn in as the pump diaphram cycles in and out. A pump without a vent (closed cavity) will have a dampening effect on the back side of the diaphram. This is beause as the diaphram moves into the cavity, back side pressure increases. When it pulses the oposite direction there is vacuum in the back side cavity. This slight pressure change can dampen/slow the diaphram pulse. Is it enough to make a difference? Maybe, if your close to using all the fuel that the pump can deliver, and make a change that could reduce the output even slightly. On a "long" WOT pull, the float levels could start to drop causing a lean condition. Backing out of the throttle slightly would reduce the engine's demand for fuel and allow the pump to "catch up". Larger main jets, puts more demand on the fuel pump, because it has to feed even more fuel flow to keep those bowls at the proper level.
Fuel pumps that are designed with no vent hole will still have this dampening effect, however the engineer will factor this in, when he/she designs the pump. This can be done by making the pump larger, larger back side cavity, etc.
A properly operating pump will put out it's rated flow, with or without a vent hole, if that was the way it was engineered. Make a change to it ,, hard to say what it will put out.
My sled is piped, I figure why take a chance, when elevating the pump off the tunnel fixes the problem.
Whew! sorry guys, I'll get off the soap box now!
Fuel pumps that are designed with no vent hole will still have this dampening effect, however the engineer will factor this in, when he/she designs the pump. This can be done by making the pump larger, larger back side cavity, etc.
A properly operating pump will put out it's rated flow, with or without a vent hole, if that was the way it was engineered. Make a change to it ,, hard to say what it will put out.
My sled is piped, I figure why take a chance, when elevating the pump off the tunnel fixes the problem.

ducky_d
Member
- Joined
- May 21, 2003
- Messages
- 32
And what about unhooking the hoses from the airbox and let them hang down free, (carb vents).
I mean the article in last/next last snowtech ?
I mean the article in last/next last snowtech ?
rx1mtn
New member
I had this problem last year on my 02 Viper, and all I did was cut a rubber foam mat the size of my fuel pump and mounted it under the pump. The foam was 3/16" thick. Worked great and the vent hole was still open but to the foam.
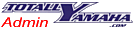
I think the easiest way to do this is as the tech section says, double nut and space it up or plug the whole......my thoughts
Mac
Member
Guys if your on the trail when you have a fuel freeze problem. Line everybody up and run a train on the fuel pump. Everybody take a piss on the pump warms it up nicly and off you go. I ride with several vipers we had to do this more than once. --mac--
ducky_d
Member
- Joined
- May 21, 2003
- Messages
- 32
Maybe if it was a artic cat, but i wont piss on my yammie.
Rather walk then...

Rather walk then...



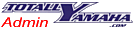
I agree Ducky...LMAO
Mac
Member
O.K. guys pissing on BLUE isn't right. I'd much rather be pissed off than pissed on any day. --mac--