
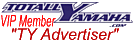
2ooosrx
VIP Member
- Joined
- Oct 2, 2004
- Messages
- 2,414
- Age
- 36
- Location
- Gurnee, Illinois
- Website
- www.cbperformanceparts.com
Well guys, here is about where I got today after a long day at work. We have recently been redesigning aspects of our belt drive design to save more weight and get more performance out of it. One of the things we are trying out is mounting the rotor on the drive axle to dramatically reduce the inertial forces of the drive line. This change required a suspension change due to the W-arm getting in the way on the standard pro-action suspension. It also involved using an apex style brake caliper because the SRX style caliper is so wide. Here are some of the pictures I have for the day. Keep in mind the stock SRX 00 and older brake caliper is about 4.5 pounds. My stock one weighed about half a pound less due to the machining of the rotor.








Last edited:

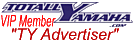
2ooosrx
VIP Member
- Joined
- Oct 2, 2004
- Messages
- 2,414
- Age
- 36
- Location
- Gurnee, Illinois
- Website
- www.cbperformanceparts.com
Other then moving the rotating mass to 1 shaft, what would be the advantage to this?
That looks painful to change brake pads
Very creative though
That looks painful to change brake pads

Very creative though
valin
Active member
The advantage to having the brake on the driveshaft is that you can still stop if you break a chain. However, I'd be skeptical as to how well it will work on a trail sled, with all the snow and ice. It works well on my race sled, but it obviously does not go in the snow.
Let us know how you make out.
Let us know how you make out.
toydoc
Member
You do some very nice work! Love all the ides you have. Plus you can make it yourself!
IMO, With the stock drivers your going to need all 4 if the sled has any power and studs. You could go with anti ratchets, but still would want outside idlers. Also the shafts won't last long.
IMO, With the stock drivers your going to need all 4 if the sled has any power and studs. You could go with anti ratchets, but still would want outside idlers. Also the shafts won't last long.

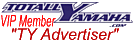
2ooosrx
VIP Member
- Joined
- Oct 2, 2004
- Messages
- 2,414
- Age
- 36
- Location
- Gurnee, Illinois
- Website
- www.cbperformanceparts.com
tomseal6 said:Other then moving the rotating mass to 1 shaft, what would be the advantage to this?
That looks painful to change brake pads
Very creative though
http://snowmobile.off-road.com/snow...a-and-lightweight-snowmobile-parts-20232.html
Take a look at this article. The advantage of placing the rotor on the drive axle deals has to do with the reduction of RPM due to the gearing change. The less RPM you have to spin the rotor at, the less amount of HP is consumed by inertial forces. Another thing to consider is that this is rotating weight that deals with moments of inertia. By reducing the total weight of the rotor as much as we did with our full floating rotor and by reducing the diameter, the amount of HP consumption will be extremely minimal on the drive axle compared to the jackshaft. In the equation for moment of inertia, the radius is squared. So by reducing the rotor diameter from ~8 5/8" to ~6 3/4", it will have a squared affect on the HP consumption. So by using this rotor being ~3 pounds lighter than stock, having a smaller diameter, and locating it on the driveaxle with lower RPM's, the HP consumption by inertial forces is reduced a considerable amount. The trade off of this that is yet to be determined is that the fact that energy does not just disappear. This means the brake pads are going to be the item that will suffer. Our question is how quickly, which will soon be determined.
Other side advantages to this is extended belt life on the belt drive by not using the belt to transfer the torque to stop the sled because the rotor is now on the driveaxle. Another advantage is if the belt ever breaks, I will still be able to walk away alive. We have done testing with the belt drive for well over 2000 miles now and the belt lasts and handles the HP of my SRX. The exact same belt drive system was placed on NOSPRO's 780? big bore SRX asphalt sled and he dropped nearly 0.3 seconds off his 1/4 time with the belt drive alone.
toydoc said:You do some very nice work! Love all the ides you have. Plus you can make it yourself!
IMO, With the stock drivers your going to need all 4 if the sled has any power and studs. You could go with anti ratchets, but still would want outside idlers. Also the shafts won't last long.
As far as the drive axle and drive cogs, this setup has been run on my SRX for well over 2000 miles. When we first started the testing with the aluminum driveaxle, we used the existing ~1" diameter splines and the axle lasted ~200 miles of very hard pulls on ice with a racing track. The axle was then inspected to find a pretty good twist in the shaft at the splines but it never snapped. Since then, we changed from ~1" splines to 1.25" splines which tremendously increased the strength. This is because when calculating torsional strength, diameter is to the 4th power. So increasing from 1" to 1.25" double the strength of the axle. With that change, we also upgraded the quality of aluminum being used for the driveaxle. With all that said, the newly design driveaxle can handle just about anything you throw at it and it has on my SRX for a long time.
As for the two drive cogs, this setup has also been extensively tested on my SRX and the sled has not had any track tension problems or ratcheting problems with this setup. The aluminum tube that connects the two cogs plays a key role in preventing this by not allowing one driver to twist in front of the other drive under load, which could lead to track ratcheting.
Thanks for the comments guys and I hope this cleared up any confusion or doubts.
-Matt
is that a full floating rotor?
2ooosrx said:http://snowmobile.off-road.com/snow...a-and-lightweight-snowmobile-parts-20232.html
Take a look at this article. The advantage of placing the rotor on the drive axle deals has to do with the reduction of RPM due to the gearing change. The less RPM you have to spin the rotor at, the less amount of HP is consumed by inertial forces. Another thing to consider is that this is rotating weight that deals with moments of inertia. By reducing the total weight of the rotor as much as we did with our full floating rotor and by reducing the diameter, the amount of HP consumption will be extremely minimal on the drive axle compared to the jackshaft. In the equation for moment of inertia, the radius is squared. So by reducing the rotor diameter from ~8 5/8" to ~6 3/4", it will have a squared affect on the HP consumption. So by using this rotor being ~3 pounds lighter than stock, having a smaller diameter, and locating it on the driveaxle with lower RPM's, the HP consumption by inertial forces is reduced a considerable amount. The trade off of this that is yet to be determined is that the fact that energy does not just disappear. This means the brake pads are going to be the item that will suffer. Our question is how quickly, which will soon be determined.
Other side advantages to this is extended belt life on the belt drive by not using the belt to transfer the torque to stop the sled because the rotor is now on the driveaxle. Another advantage is if the belt ever breaks, I will still be able to walk away alive. We have done testing with the belt drive for well over 2000 miles now and the belt lasts and handles the HP of my SRX. The exact same belt drive system was placed on NOSPRO's 780? big bore SRX asphalt sled and he dropped nearly 0.3 seconds off his 1/4 time with the belt drive alone.
As far as the drive axle and drive cogs, this setup has been run on my SRX for well over 2000 miles. When we first started the testing with the aluminum driveaxle, we used the existing ~1" diameter splines and the axle lasted ~200 miles of very hard pulls on ice with a racing track. The axle was then inspected to find a pretty good twist in the shaft at the splines but it never snapped. Since then, we changed from ~1" splines to 1.25" splines which tremendously increased the strength. This is because when calculating torsional strength, diameter is to the 4th power. So increasing from 1" to 1.25" double the strength of the axle. With that change, we also upgraded the quality of aluminum being used for the driveaxle. With all that said, the newly design driveaxle can handle just about anything you throw at it and it has on my SRX for a long time.
As for the two drive cogs, this setup has also been extensively tested on my SRX and the sled has not had any track tension problems or ratcheting problems with this setup. The aluminum tube that connects the two cogs plays a key role in preventing this by not allowing one driver to twist in front of the other drive under load, which could lead to track ratcheting.
Thanks for the comments guys and I hope this cleared up any confusion or doubts.
-Matt
awsome job....that a nice set up ...but what happend went the brake and rotor will be full of ice and snow ??does it will break or just slide .....great set up for asphalt racing

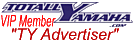
2ooosrx
VIP Member
- Joined
- Oct 2, 2004
- Messages
- 2,414
- Age
- 36
- Location
- Gurnee, Illinois
- Website
- www.cbperformanceparts.com
Yes it is.KneeDown said:is that a full floating rotor?
As far as the braking in the snow and ice, I guess time will only tell but my theory is this. Does your car stop in the rain and snow? Like I said, I understand that ice could build up but the same theory applies to a car. I truly can't wait to get out and test this setup though.
Thats a nice piece Bruce,
I suppose if your chain breaks at 150 MPH your about to have a very bad day without this system.
I suppose if your chain breaks at 150 MPH your about to have a very bad day without this system.
mattyg1405
New member
i think in all but extreme cold you should be fine that brake rotor and caliper will generate heat almost instantly when being used... you could always come up with some kind of gaurd or cover too to protect from ice and hold some heat in2ooosrx said:Yes it is.
As far as the braking in the snow and ice, I guess time will only tell but my theory is this. Does your car stop in the rain and snow? Like I said, I understand that ice could build up but the same theory applies to a car. I truly can't wait to get out and test this setup though.
PZ 1
Member
- Joined
- Mar 12, 2005
- Messages
- 987
The problem would be if the caliper freezes tight with ice and will not move when the brakes are applied. True that it doesn't happen on a car, but it is not normal for the area where the caliper is on a car to become as ice encrusted as under the tunnel on a sled, and if one does freeze, there are three others to stop with. - Not saying that it will happen, and great if it doesn't.
The trade off for improved acceleration performance will be reduced brake performance because of the reduced speed and reduced diameter of the disc. That will require increased brake lever pressure to stop the sled. There will be more heat buildup and stopping distances will be longer. The increased heat will be somewhat offset by the better cooling of the brake assembly.
The trade off for improved acceleration performance will be reduced brake performance because of the reduced speed and reduced diameter of the disc. That will require increased brake lever pressure to stop the sled. There will be more heat buildup and stopping distances will be longer. The increased heat will be somewhat offset by the better cooling of the brake assembly.
toydoc
Member
2ooosrx said:http://snowmobile.off-road.com/snow...a-and-lightweight-snowmobile-parts-20232.html
Take a look at this article. The advantage of placing the rotor on the drive axle deals has to do with the reduction of RPM due to the gearing change. The less RPM you have to spin the rotor at, the less amount of HP is consumed by inertial forces. Another thing to consider is that this is rotating weight that deals with moments of inertia. By reducing the total weight of the rotor as much as we did with our full floating rotor and by reducing the diameter, the amount of HP consumption will be extremely minimal on the drive axle compared to the jackshaft. In the equation for moment of inertia, the radius is squared. So by reducing the rotor diameter from ~8 5/8" to ~6 3/4", it will have a squared affect on the HP consumption. So by using this rotor being ~3 pounds lighter than stock, having a smaller diameter, and locating it on the driveaxle with lower RPM's, the HP consumption by inertial forces is reduced a considerable amount. The trade off of this that is yet to be determined is that the fact that energy does not just disappear. This means the brake pads are going to be the item that will suffer. Our question is how quickly, which will soon be determined.
Other side advantages to this is extended belt life on the belt drive by not using the belt to transfer the torque to stop the sled because the rotor is now on the driveaxle. Another advantage is if the belt ever breaks, I will still be able to walk away alive. We have done testing with the belt drive for well over 2000 miles now and the belt lasts and handles the HP of my SRX. The exact same belt drive system was placed on NOSPRO's 780? big bore SRX asphalt sled and he dropped nearly 0.3 seconds off his 1/4 time with the belt drive alone.
As far as the drive axle and drive cogs, this setup has been run on my SRX for well over 2000 miles. When we first started the testing with the aluminum driveaxle, we used the existing ~1" diameter splines and the axle lasted ~200 miles of very hard pulls on ice with a racing track. The axle was then inspected to find a pretty good twist in the shaft at the splines but it never snapped. Since then, we changed from ~1" splines to 1.25" splines which tremendously increased the strength. This is because when calculating torsional strength, diameter is to the 4th power. So increasing from 1" to 1.25" double the strength of the axle. With that change, we also upgraded the quality of aluminum being used for the driveaxle. With all that said, the newly design driveaxle can handle just about anything you throw at it and it has on my SRX for a long time.
As for the two drive cogs, this setup has also been extensively tested on my SRX and the sled has not had any track tension problems or ratcheting problems with this setup. The aluminum tube that connects the two cogs plays a key role in preventing this by not allowing one driver to twist in front of the other drive under load, which could lead to track ratcheting.
Thanks for the comments guys and I hope this cleared up any confusion or doubts.
-Matt
Cool, like the size jump to 1.25 on the splines. Looks like the track has 144 studs. If you put in a race track load it up with chisels, setup for a good hole shot. Two drivers will be a issue. Even with four drivers they still jump.
This is a shaft with 168 hp, but good race hole shot:
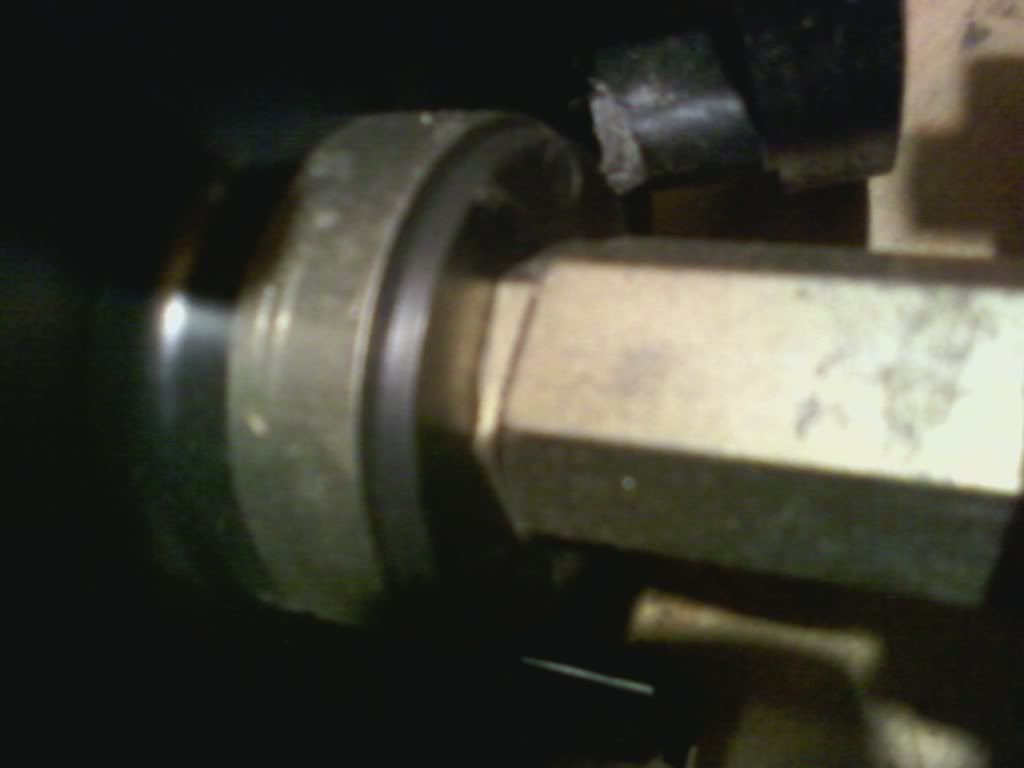
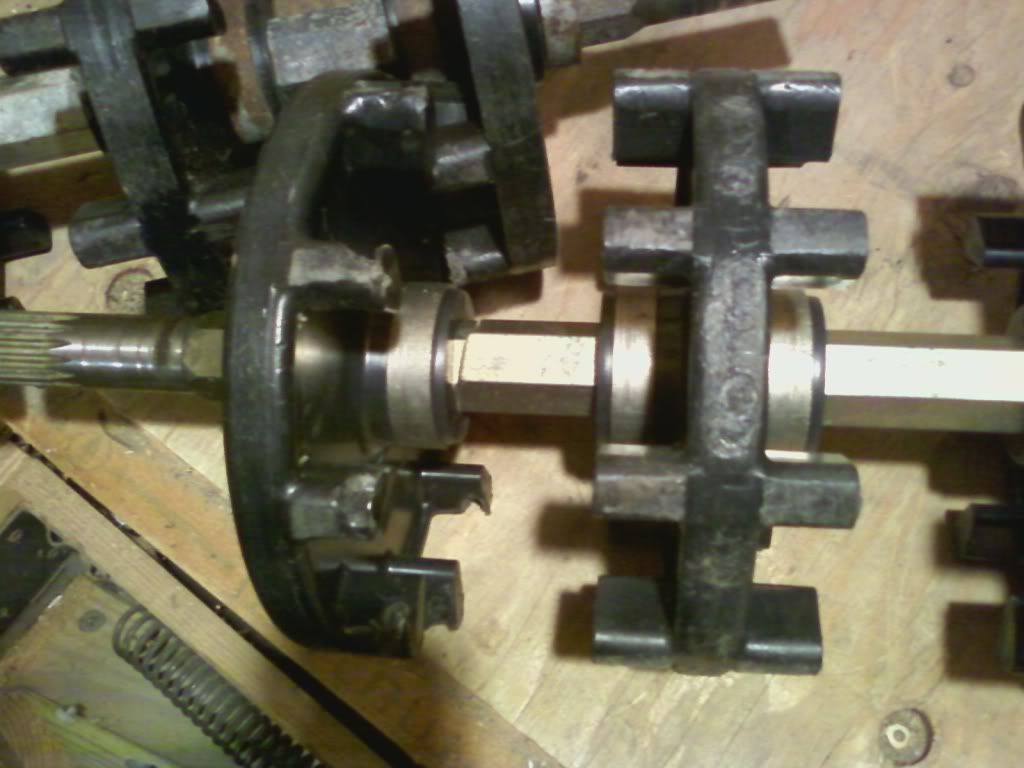
Ti shaft thats starting to turn the splines (my second Ti shaft, first is to far gone).
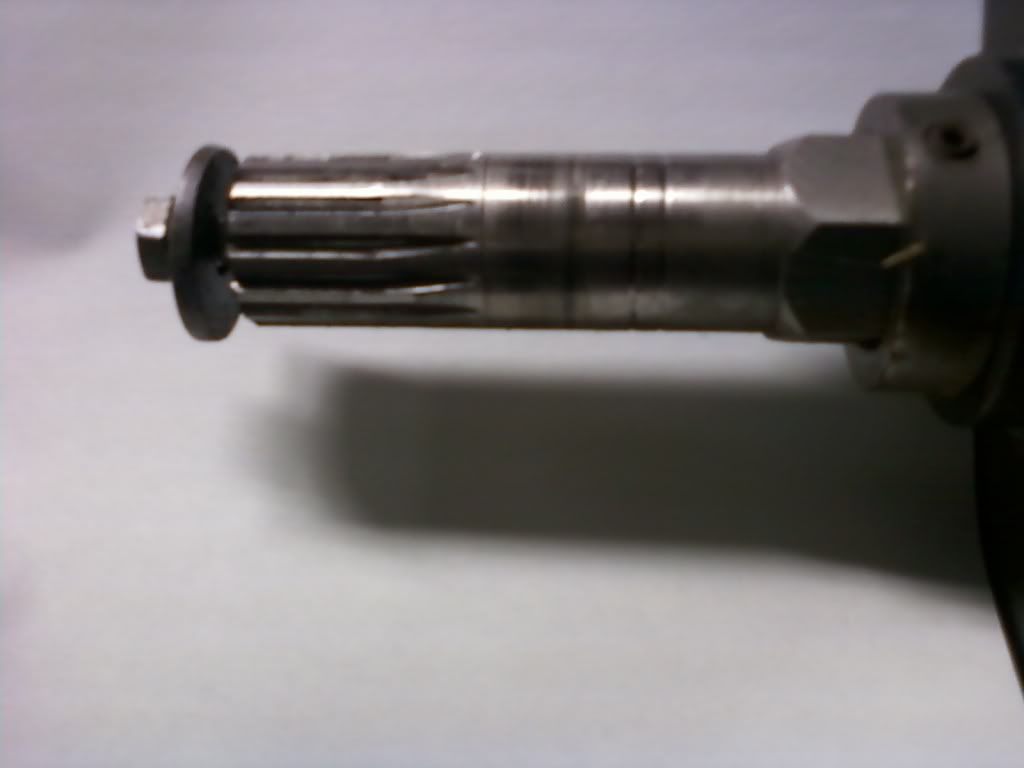
2ooosrx said:
Being a newb this pic helps me in understanding some things,. but I would like to ask for clarification The "upper " shaft, is that called the jackshaft or driveshaft, or vice versa.. I notice the assembly over to the right has a shorter belt connecting the 2 shafts to transfer power. Is that usually replaced bu the chain in the chaincase in a stock sled? The left end of the upper shaft is what goes through the secondary? The 2 plastic things are what are "inside" the rotation of the track and what "drive" the track?
Last edited:

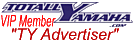
2ooosrx
VIP Member
- Joined
- Oct 2, 2004
- Messages
- 2,414
- Age
- 36
- Location
- Gurnee, Illinois
- Website
- www.cbperformanceparts.com
The upper shaft is called the jackshaft and the lower shaft is called the Driveaxle. The belt drive on the right side is a design used to replace the entire chaincase on a stock snowmobile. The Left end of the upper shaft goes to the secondary. Lastly, the plastic wheels are drive cogs which transfer the power to the track.
As far as the track ratcheting, I have not had any issues with it with a zero spin hole shot before. My engagement does not come in like a drag racing setup (mine is ~4200) but the sled still has some ball to it. We have had the 1.25" spline axle in for many miles with hard hole shots without any problems or signs of twist in the shaft. The track I run in my sled is a 9811R with 1" studs so when I get on ice, it doesn't tend to slip. I wonder if the belt drive system might be providing a forgiveness under acceleration that is allowing these results? Like I said, I have had many no track spin hole shots with this setup and the 2 drivers as well as the aluminum axle have held perfectly. Another thing to keep in mind is i am not running gearing built for 1000' races either.
As far as the track ratcheting, I have not had any issues with it with a zero spin hole shot before. My engagement does not come in like a drag racing setup (mine is ~4200) but the sled still has some ball to it. We have had the 1.25" spline axle in for many miles with hard hole shots without any problems or signs of twist in the shaft. The track I run in my sled is a 9811R with 1" studs so when I get on ice, it doesn't tend to slip. I wonder if the belt drive system might be providing a forgiveness under acceleration that is allowing these results? Like I said, I have had many no track spin hole shots with this setup and the 2 drivers as well as the aluminum axle have held perfectly. Another thing to keep in mind is i am not running gearing built for 1000' races either.
montynormand
Member
Very Nice Work. I have been wanting to put the brake rotor on the drive shaft of my SRX600 all summer, but just never found the time
This is very, very cool.




mattyg1405
New member
2ooosrx said:The upper shaft is called the jackshaft and the lower shaft is called the Driveaxle. The belt drive on the right side is a design used to replace the entire chaincase on a stock snowmobile. The Left end of the upper shaft goes to the secondary. Lastly, the plastic wheels are drive cogs which transfer the power to the track.
As far as the track ratcheting, I have not had any issues with it with a zero spin hole shot before. My engagement does not come in like a drag racing setup (mine is ~4200) but the sled still has some ball to it. We have had the 1.25" spline axle in for many miles with hard hole shots without any problems or signs of twist in the shaft. The track I run in my sled is a 9811R with 1" studs so when I get on ice, it doesn't tend to slip. I wonder if the belt drive system might be providing a forgiveness under acceleration that is allowing these results? Like I said, I have had many no track spin hole shots with this setup and the 2 drivers as well as the aluminum axle have held perfectly. Another thing to keep in mind is i am not running gearing built for 1000' races either.
do you sell the belt drive system?

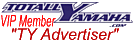
2ooosrx
VIP Member
- Joined
- Oct 2, 2004
- Messages
- 2,414
- Age
- 36
- Location
- Gurnee, Illinois
- Website
- www.cbperformanceparts.com
I believe we are going to begin marketing it very shortly as we are also currently working on the design for the Apex as well. There will probably be both a race and trail version of the system with different total components.
montynormand
Member
2ooosrx said:I believe we are going to begin marketing it very shortly as we are also currently working on the design for the Apex as well. There will probably be both a race and trail version of the system with different total components.
Well if you need a test pilot for the 2012 race season, I know a Guy!!!!
Millennium Technologies; Liberty Traction (Studboy); Heinens Yamaha; and CB Performance..... Would make for a nice sponsorship package.
Now that I am running late model stuff with ORA - I could use all the help I can get!
http://www.snowmobileracing.mn/